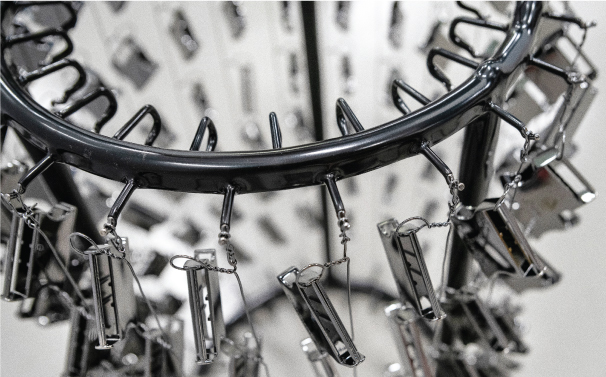
Galvanica statica
La galvanica statica è la scelta migliore per conferire massima qualità agli accessori. Si utilizzano principalmente materiali preziosi come palladio, oro e rutenio. L’aggancio manuale dei singoli pezzi a telai specifici evita le possibili collisioni tra loro e garantisce il mantenimento delle superfici lisce e perfette.
Galvanica statica
Galvanica a rotobarile
PVD
Sputtering
Verniciatura
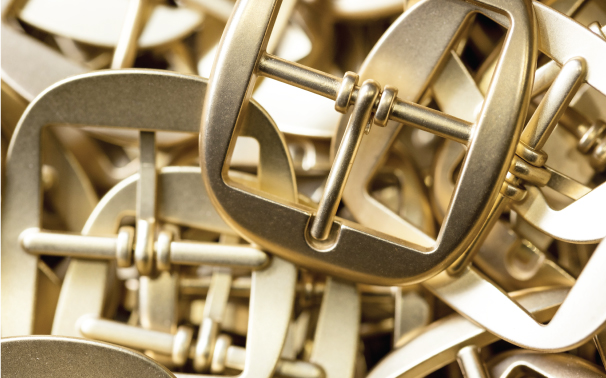
Galvanica rotobarile
La galvanica rotobarile è la tecnica più tradizionale ed è indicata maggiormente per il trattamento di piccoli accessori e loro sottoparti. Le quattro linee di trattamento consentono di ottenere una vasta gamma di finiture.
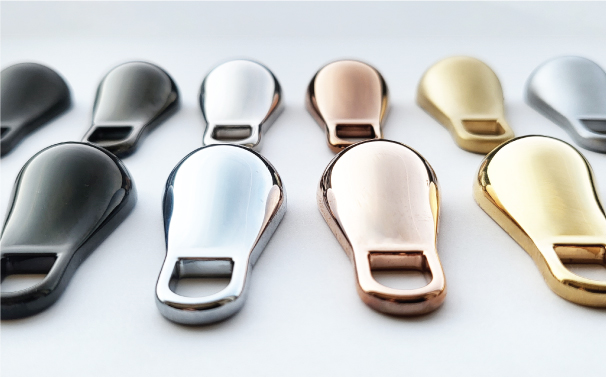
PVD
I rivestimenti in PVD sono indicati per quei prodotti innovativi e tecnicamente avanzati che necessitano elevate prestazioni di resistenza all’abrasione, al graffio e alla corrosione. Trattandosi di un trattamento fisico e non chimico questo tipo di rivestimento è considerato perfettamente sostenibile e a ridotto impatto ambientale.
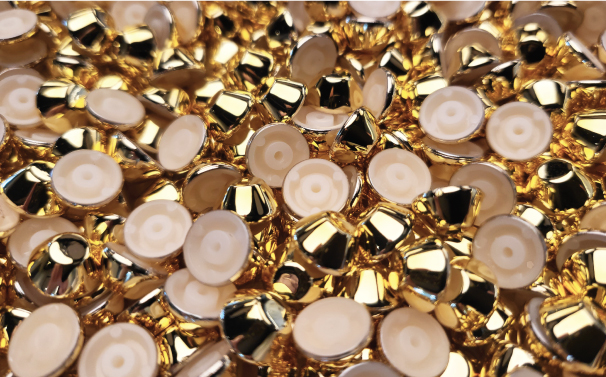
Sputtering
Lo sputtering è una lavorazione asciutta che agisce a bassa temperatura e consente di applicare metallo vaporizzato sulle superfici. È un metodo di deposizione sottovuoto estremamente versatile.
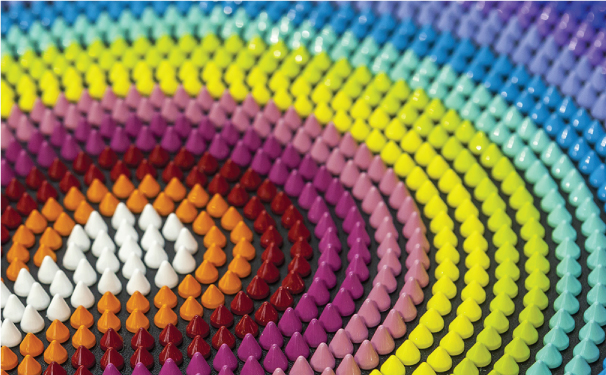
Verniciatura
La verniciatura permette di ottenere aspetti cromatici vivaci e variopinti. Infinito è il ventaglio di colori oltre agli effetti di lucentezza, gommatura o opacità.